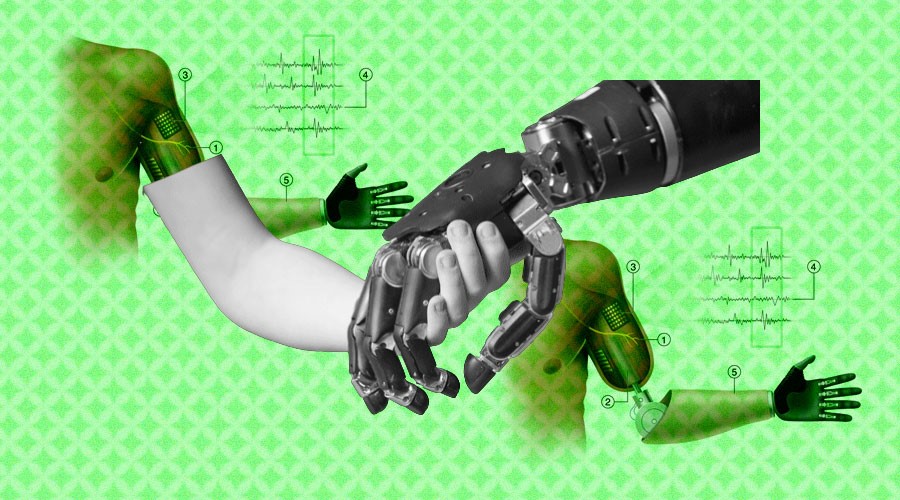
Advanced New Sensors Could Transform Prosthetics and Robotic Limbs
Summary:
Abstract: Ultra-Thin Graphene Foam Based Flexible Piezoresistive Pressure Sensors for Robotics Over recent year, robotics has made a drastic impact in a variety of different markets. Although having many advantages from, safer workspace to speed and efficiency there are several drawbacks all ranging from their lack of ability to execute functions and tasks easily performed by humans. This is mainly due to their lack of ability to implement touch and haptic feedback. In this work, we show the use and applicability of ultra-thin graphene foam (GRF), with polydimethylsiloxane (PDMS) embedded into and over the structure, as an active layer in piezoresistive based pressure sensors for use in robotic touch sensing applications. It has been demonstrated in this work that thin GRF/PDMS-GRF consisting of a few layers of graphene is able to present sensitivity to pressures within the range of 0 to >100kPa. Although pressure sensitivities are not yet comparable to those of current work, it must be noted that the GRF used in this work is much thinner in comparison, consisting of only several layers of graphene.
The innovative research project aspires to develop sensors that provide enhanced capabilities to robots, helping improve their motor skills and dexterity, through the use of highly accurate pressure sensors that provide haptic feedback and distributed touch. It is led by the University of the West of Scotland (UWS), Integrated Graphene Ltd, and supported by the Scottish Research Partnership in Engineering (SRPe) and the National Manufacturing Institute for Scotland (NMIS) Industry Doctorate Programme in Advanced Manufacturing.
The innovative research project aspires to develop sensors that provide enhanced capabilities to robots, helping improve their motor skills and dexterity, through the use of highly accurate pressure sensors that provide haptic feedback and distributed touch. It is led by the University of the West of Scotland (UWS), Integrated Graphene Ltd, and supported by the Scottish Research Partnership in Engineering (SRPe) and the National Manufacturing Institute for Scotland (NMIS) Industry Doctorate Programme in Advanced Manufacturing.
Professor Des Gibson, Director of the Institute of Thin Films, Sensors and Imaging at UWS and project principal investigator, said: “Over recent years the advancements in the robotics industry have been remarkable, however, due to a lack of sensory capabilities, robotic systems often fail to execute certain tasks easily. For robots to reach their full potential, accurate pressure sensors, capable of providing greater tactile ability, are required.
“Our collaboration with Integrated Graphene Ltd, has led to the development of advanced pressure sensor technology, which could help transform robotic systems.”
Made from 3D graphene foam, which offers unique properties when put under mechanical stress, the sensors use a piezoresistive approach. This means that when the material is put under pressure it dynamically changes its electric resistance, easily detecting and adapting to the range of pressure required, from light to heavy.
Marco Caffio, co-founder and Chief Scientific Officer at Integrated Graphene said: “Gii, our novel 3D graphene foam, has the capability to mimic the sensitivity and feedback of human touch, which could have a transformative impact on how robotics can be used for a whole range of real-world applications from surgery to precision manufacturing.
“We know the unique property of Gii makes it suitable for use in other applications like disease diagnostics and energy storage, so we’re always very excited to be able to demonstrate its flexibility in projects like this one.”
Dr. Carlos Garcia Nunez, School of Computing Engineering and Physical Sciences at UWS added: “Within robotics and wearable electronics the use of pressure sensors is a vital element, to provide either an information input system, or to give robotic systems human-like motor skills. An advanced material like 3D graphene foam offers excellent potential for use in such applications, due to its outstanding electrical, mechanical, and chemical properties.
“Our work shines a light on the significant potential for this technology to revolutionize the robotics industry with dynamic pressure sensors.”
Claire Ordoyno, Interim Director of SRPe, stated: “The SRPe – NMIS Industrial Doctorate Programme brings together groundbreaking academic research with industry partners to drive forward innovation in engineering. These collaborative PhD projects not only enhance the Scottish engineering research landscape, but produce innovation focussed, industry-ready PhD graduates to feed the talent pipeline.”
The next stage of the project – funded by UWS, Integrated Graphene Ltd, SRPe and NMIS – will look to further increase sensitivity of the sensors, before developing for wider use in robotic systems.
Reference: “Ultra-Thin Graphene Foam Based Flexible Piezoresistive Pressure Sensors for Robotics” by Connor I. Douglas, Carlos Garcia Nuñez, Marco Caffio and Des Gibson, June 2022, Key Engineering Materials. DOI: 10.4028/p-oy94hj